将废物塑料转变为有价值的再生塑料颗粒,既是环保计划,也是一项有利可图的企业。从农业膜和包装材料到诸如桶,玩具和汽车零件等日常物品的废物塑料可以在专用机械的帮助下将其加工成高质量的颗粒。
在以下各节中,我们将概述该过程,并强调塑料颗粒者在建立成功的回收业务中所发挥的关键作用。
再生塑料颗粒的基本设备
为了开始再生的颗粒操作,投资塑料颗粒剂至关重要。该机器是生产线的核心,将清洁和压碎的塑料废料转化为一致的颗粒,可以有效地处理聚乙烯(PE)和聚丙烯(PP)等材料。
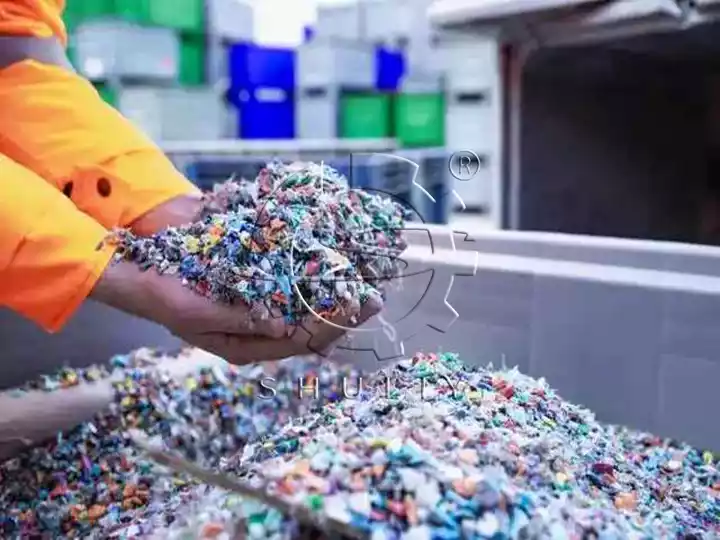
关键特性
- 可靠的挤压系统可确保均匀的熔化和混合。
- 节能供暖减少了运营费用。
- 可调节的切割机制可自定义的颗粒大小。
辅助设备
- 破碎机:通过将塑料分解成2-3毫米薄片来制备废料,从而促进了更平滑的挤出过程。
- 馈线:提供自动大规模操作的材料输入。
- 冷却和包装系统:确保颗粒稳定并为市场做好准备。
生产再生颗粒的逐步过程
步骤 1:材料清洗和分类
塑料废物经常包括污染物,例如污垢,标签或残留物。适当的清洁和分类保证只有在生产线上处理清洁,均匀的材料。此过程提高了颗粒质量并减少机器磨损。
步骤 2:破碎以获得均匀的尺寸
破碎机通过将干净的塑料分解成小薄片来提高颗粒机的熔融效率。保持一致的薄片大小有助于防止堵塞并确保在挤出过程中加热分布。
步骤 3:熔化和挤出
该过程的核心是塑料颗粒剂。熔融塑料流过模具,形成条。水冷却系统迅速冷却并切割回收的塑料颗粒,使它们固化以进行存储和运输。
步骤 4:包装以准备上市
将干球员称重并用自动化系统包装,以确保它们符合塑料产品制造商转售的行业标准。
您可以通过HDPE PP PS 硬刚性废塑料颗粒化回收线查看塑料造粒的详细过程。
为什么投资塑料颗粒机?
在包括纺织品和建筑在内的各个行业都高度追捧回收的塑料颗粒。将颗粒剂纳入您的回收设施可以提供许多好处。通过将廉价废物转换为优质原材料来提高您的盈利能力。
无论您是在处理塑料瓶、薄膜还是工业废物,这项技术都提供了一种可扩展的解决方案,以应对循环经济倡议日益增长的需求。了解我们的颗粒机选择,今天就开始建立您的可持续业务!