The tire steel wire separator is designed to effectively separate tire bead wire by managing the speed ratio of the groove roller. This process not only preserves the physical properties of the steel wire but also ensures that the rubber recycling is pollution-free. It’s perfect for small car tires (up to 800mm), engineering tires (starting from 900mm), as well as radial and bias tires, among other types.
Whether you’re dealing with pneumatic or solid tires, this tire steel wire separator machine makes it easy to obtain high-purity raw materials for remanufacturing steel wire and processing rubber. It efficiently removes most rubber particles from the steel wire, achieving an impressive 95-98% separation rate, leaving just 2-3% of residual rubber in the steel wire.
scrap tire Bead wire separator main features
- The wear parts are made of wear-resistant steel plate, which improves the overall wear resistance and effectively reduces the maintenance cycle and cost of the equipment.
- The knives can be disassembled independently, short replacement time and speed; the fixed knives can be used for many times for maintenance, long service life.
- Precise stripping of bead steel wire, complete retention of the physical properties of steel wire, to ensure the subsequent reuse value.
- Compatible with small car tires, large car tires, pneumatic/solid tires and radial/bias tires, covering all kinds of tire processing needs.
- Steel – rubber separation process without chemical pollution, rubber can be secondary deep processing, steel wire directly back to the furnace regeneration, truly realize the closed-loop utilization of resources.
- Integrated extrusion separation process, low energy consumption per unit, high processing efficiency, greatly reducing the cost of manual dismantling and safety risks.
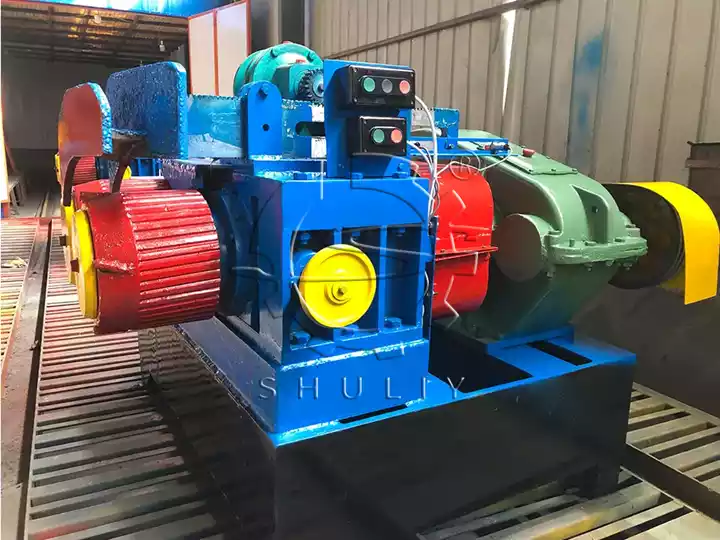
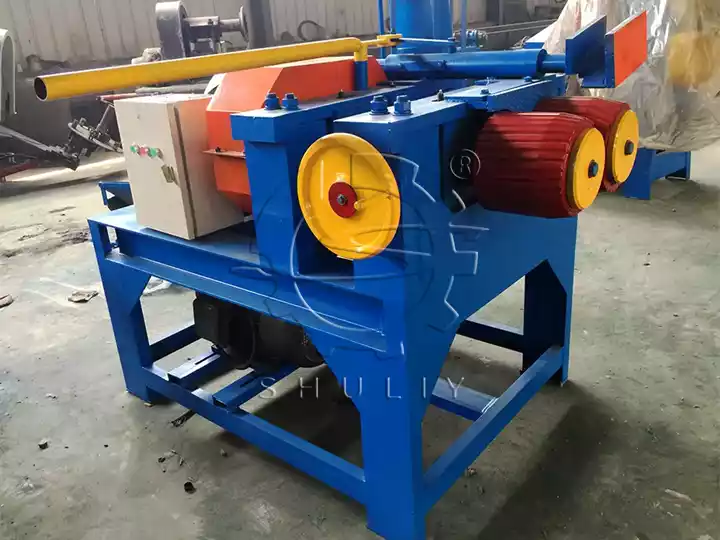
Tire steel wire removing machine applications
- Used for tire recycling pre-processing for scenes such as waste tire dismantling centers, rubber recycling plants, metal recycling stations, etc.
- Extended application for precise sorting of metal and non-metal mixed waste (such as rubber products, industrial belts, etc.).
- Drive rubber regeneration, steel wire back to the furnace and environmental protection industry chain closure through steel – rubber zero pollution separation.
- Meet the environmental requirements of no exhaust gas, waste water, waste residue emission, applicable to industrial zones or renewable resources processing bases that need to comply with strict environmental regulations.
working principle of tire steel wire separator
The core components of this tire steel wire separator machine consist of two rollers that rotate in sync. When a tire rim is fed into the space between these rollers, it gets compressed by them.
At the same time, the rim experiences squeezing, shearing, and tearing due to the action of the rollers. This process continues until the steel wheel is completely separated after several cycles.
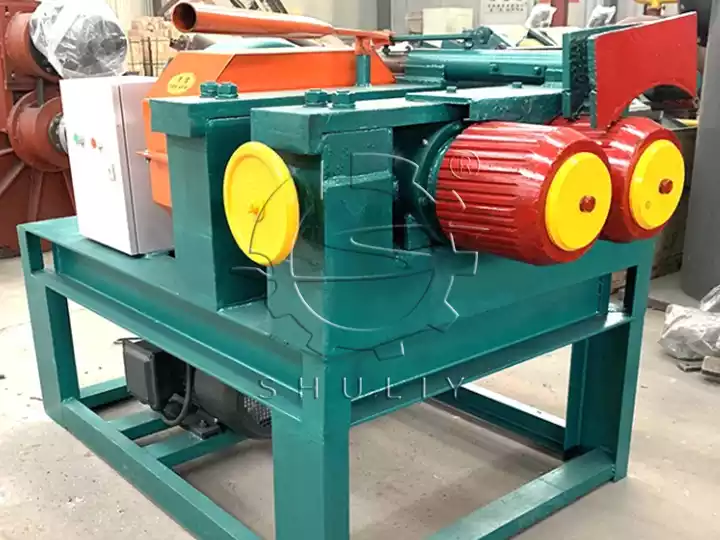
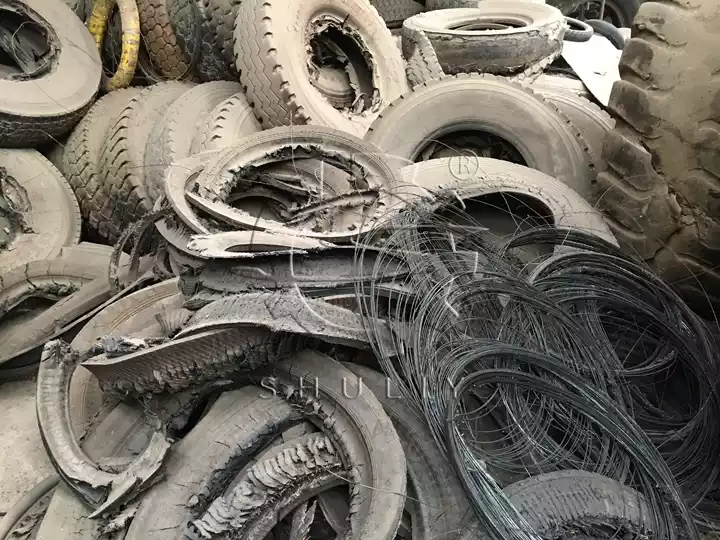
steel ring separating machine techincal data
Model No. | SWS-100 Steel wire separator |
Motor power | 18.5KW |
Capacity | 120pcs/h |
L*W*H | 2*1.9*1.8m |
Weight | 1800kg |
Why should you use a tire steel wire removal machine?
Traditional tire rims are separated by incineration, which is inefficient and polluting – the high temperature leads to annealing of the steel wire, losing the core value of high elasticity and hardness, and the rubber cannot be reused due to carbonization.
The tire steel wire separator breaks the mold with the innovative double groove roller differential speed extrusion technology:
- By adjusting the speed ratio of groove rollers, the steel wire and rubber are precisely separated, ensuring that the steel wire maintains excellent elasticity and hardness, and can be directly used in high-end scenarios such as sandblasting rings.
- The whole process has no combustion and zero exhaust gas emission, and the purity of separated rubber is ≥98%, which can meet the demand for deep processing of recycled rubber and cracked raw materials.
- Designed for batch processing of waste tires, avoiding the time-consuming problem of manual dismantling, and increasing the processing capacity of single machine by more than 3 times.
Not only that – we can also provide matching tire ring cutter machine (accurately remove sidewall beads), strips/blocks cutter machine and other equipment, forming a “cutting – separation – crushing” full-process solution. Whether you need to upgrade a single piece of equipment or automate the entire line, we can provide customized solutions and technical guidance. Contact us now!