The tire ring cutting machine is designed specifically to efficiently pre-process waste steel wire tires. It expertly cuts through sidewalls, crowns, and bead rings with precision. This equipment features a robust knife die and an intelligent slitting system, making it versatile enough to handle tires of all sizes. It ensures high-purity raw materials for oil refining and recycled rubber production. Whether you’re dealing with cars, trucks, or even engineering tires, this machine makes the work very easy!
highlights of tire ring cutting machine
- The fixed blade is crafted from top-notch tool steel, while the movable blade undergoes a high-hardness treatment, making it resistant to wear and significantly extending its lifespan—by over three times!
- Allows for quick disassembly and maintenance, cutting maintenance costs by 60%. Even those without professional training can easily get the hang of it.
- A fully automatic lifting system, minimizes the need for manual handling, enabling one person to manage the entire tire positioning and cutting process.
- The motor is 40% more energy-efficient compared to traditional equipment, and a single tire ring cutting machine can handle over 500 tires daily, boosting cutting efficiency by an impressive 200%.
- Thanks to its modular structure and lightweight design, it occupies less than 5 square meters, making it ideal for everything from small recycling facilities to large-scale processing centers and beyond.
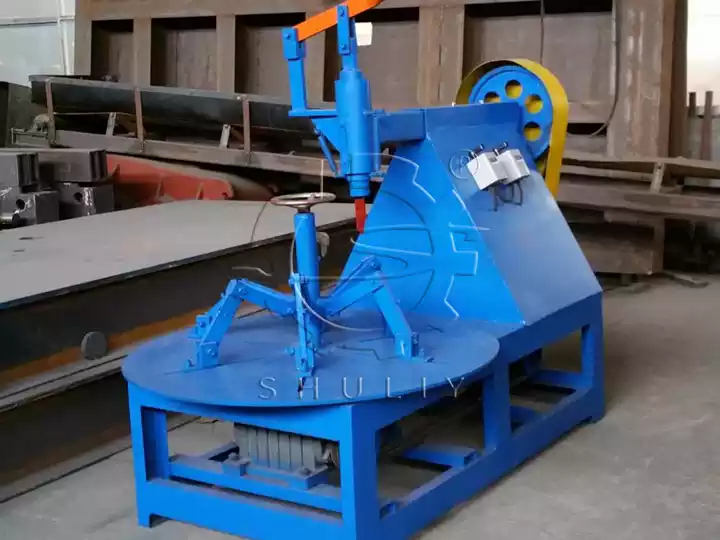
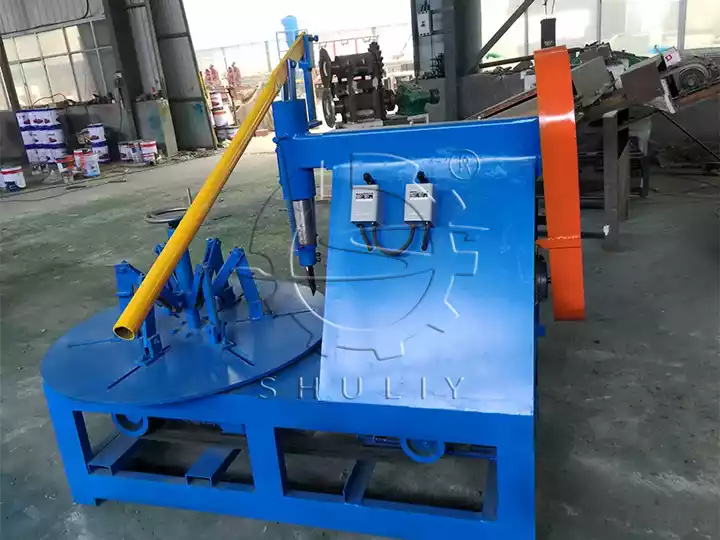
What Is A Tyre Sidewall?
The sidewalls of a tire are the vertical structures located on either side, primarily designed to keep air sealed inside, absorb impacts, and ensure stable driving. However, recycling these sidewalls poses a challenge due to the steel bead embedded within them. If the sidewalls are not removed, they can damage the shredding equipment, and their elasticity can significantly increase the energy needed for compression.
The main benefits of using a tire ring cutting machine include:
- It effectively removes the steel wire bead, protects the crushing tool, and can extend the lifespan of the equipment by over 30%.
- Tread rubber without sidewalls is much easier to compress, reducing its volume to one-fifth of the original size and cutting storage costs by 60%.
- The steel from the bead can be recycled separately, with about 2-3 kg extracted from each truck tire, and the tread rubber maintains a purity level of over 95%, making it ideal for high-value recycling.
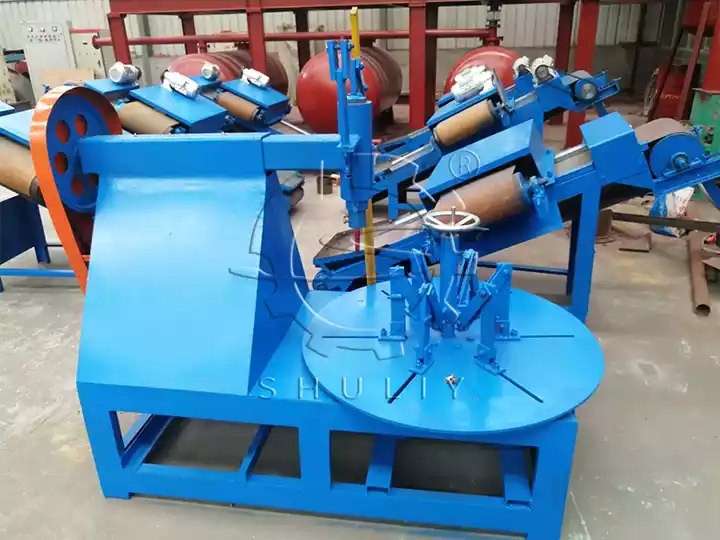
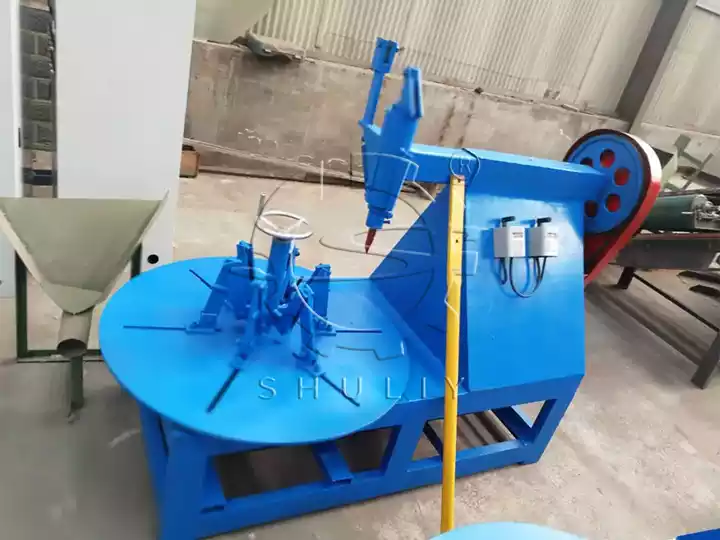
tyre sidewall cutter structure and principle
The main body of this tire ring cutting machine is made up of four essential components: a sturdy frame, a rotary drive system, a three-jaw support and positioning setup, and a flexible tool system that can be adjusted as needed.
The tire circle cutting machine is a standalone accessory designed for tires larger than 650 type, whether they are made of nylon or steel wire. It works by flattening the tire on the machine and securely locking it in place using an up-and-down locking system. Then, alloy tools are positioned to the specific area where the tire needs to be cut, allowing for the removal of the tire’s mouth and nation in just three minutes.
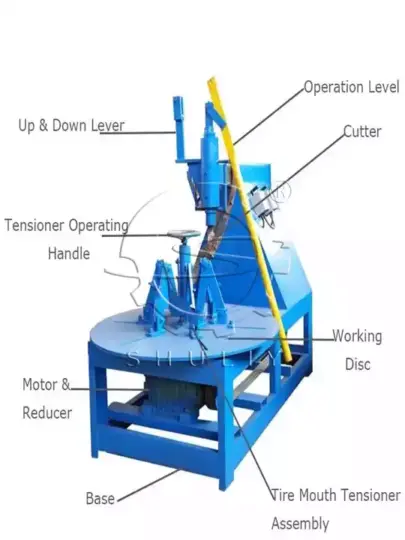
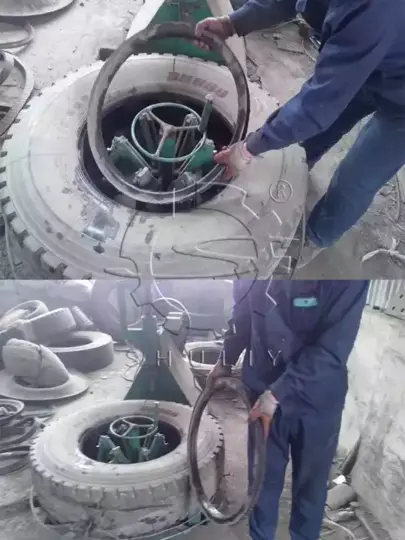
technical data of tire circle cutter machine
Name | Technical parameter |
Motor power | 4 KW+0.75KW |
Capacity | 40pcs/h |
Work range | ∮650-1250mm |
L*W*H | 1.8m*1.3m*1.6m |
Weight | 650 kg |
Why cut the sidewalls of the tyres?
Tire beads are made with high-strength steel wire belts that are coated with copper or brass. If these wires break without removing the sidewalls first, it can lead to increased tool wear and equipment failures. The bead cutter effectively separates the steel bead from the tread rubber by precisely cutting the sidewalls.
- By eliminating metal impurities during the crushing process, while providing uniform raw materials for cracking and refining.
- The magnetic separation process recovers over 98% of the bead steel wire, extracting between 0.8-1.2 kg from a single car tire.
- The rubber purity reaches over 95%, solving the issue of cross-contamination found in traditional methods.
- The tread structure is flat and uniform, which enhances crushing efficiency, reduces power consumption, and standardizes the rubber block size for regeneration processing.
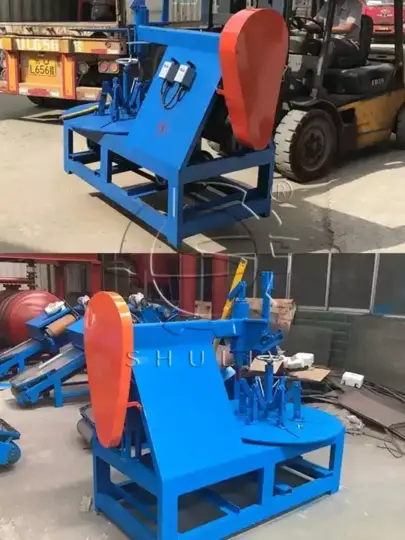
If your company is struggling with low efficiency, excessive equipment wear, and diminishing resource value, our tire ring cutting machine could be the perfect solution for you!
Whether you run a small recycling station or a large processing center handling 10,000 tons, we can suggest a cost-effective model tailored to your daily processing needs, tire specifications, and budget. We also offer free customization of process plans and on-site testing services. Don’t hesitate to reach out to us!