A máquina de britagem em pó de borracha pode converter com eficiência blocos de borracha de pneus residuais (30-100 mm) em pó de borracha fina de 5-40 malha e classificar simultaneamente o fio de aço e a fibra de nylon. Através de esmagamento em vários estágios e triagem precisa, o equipamento pode personalizar a saída de pó de borracha com diferentes tamanhos de partículas (adequado para tapetes, rodovias, borracha reciclada, pista de borracha e outros cenários), para que cada grama de borracha de pneus residuais se torne um material prato de alto valor.
Principais características da máquina trituradora de pó de borracha
- A adoção de um motor de baixa potência e um sistema de transmissão otimizado, considerando a alta capacidade e economia de energia, reduz os custos operacionais.
- O esmagamento, a triagem e a classificação são concluídos simultaneamente, separando com precisão o fio de aço (reciclagem de aço) e fibra de nylon (processamento secundário).
- As lâminas e telas esmagadoras são feitas de carboneto de tungstênio/aço de manganês alto, que é de impacto e desgaste. Isso prolonga a vida útil da máquina de britagem em pó de borracha e reduz a frequência de manutenção.
- A configuração do módulo de triagem de vibração em vários estágios suporta 5-40 malha em pó de borracha em pó (ajustável), para atender às necessidades de diferentes cenários (tapetes, asfalto, borracha reciclada, etc.).
- A tecnologia de resfriamento de água e resfriamento por ar de ar e a borracha de resfriamento de água impede que a borracha cola ou se degradasse devido à alta temperatura de esmagamento e garante a qualidade e a eficiência da produção do pó de borracha.
- A tecnologia de unidade de conversão de frequência realiza ajuste de escala de velocidade de rotação e lacuna de esmagamento, adaptando -se ao processamento de blocos de borracha de dureza diferente, com forte compatibilidade.
- Design integrado horizontal para reduzir a pegada, com uma concha de redução de ruído e base de absorção de choque, adequada para fábricas e parques ambientais intensivos em layout.
- A estrutura da desmontagem rápida das peças-chave suporta limpeza ou substituição rápida, reduz o tempo de inatividade e melhora a taxa de utilização abrangente.
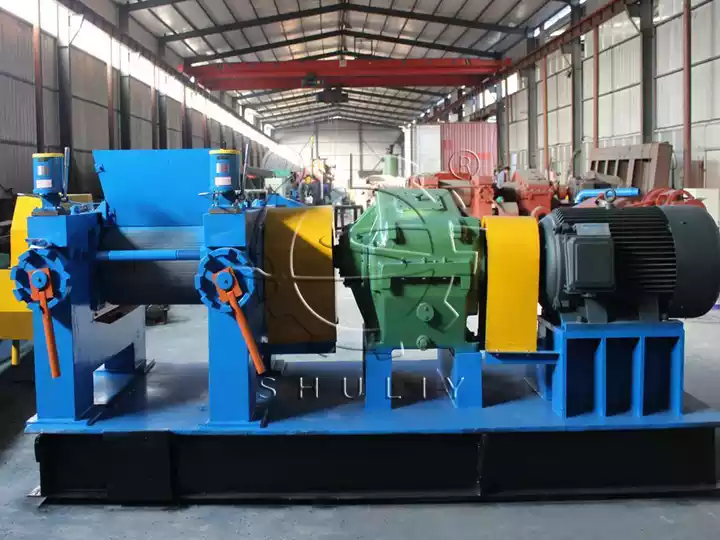
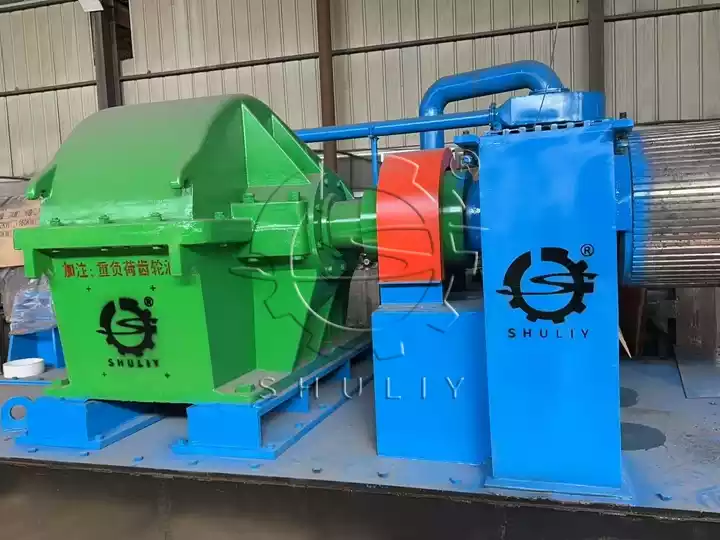
Âmbito de aplicação e cenário da linha de pó de borracha
- Construção de instalações esportivas: produza 5-40 malha em pó de borracha fina, usada para pista de corrida plástica, esteiras de terra esportiva, camada de tampão de playground infantil, para melhorar a elasticidade e a segurança.
- Materiais de construção de construção: Processando ladrilhos de borracha, placas de isolamento de som e outros produtos, adequados para 10-20 malha de borracha de grãos médios, resistente ao desgaste e ecológicos.
- Fabricação de material à prova d'água: Forneça 20-40 malha de borracha ultrafina em pó como aditivo núcleo para membrana à prova d'água e revestimento para aprimorar as propriedades da ductilidade e antienvelhecimento do material.
- Aplicações de infraestrutura de transporte: produzir pó de borracha especial de asfalto modificado (partículas grossas de 5-10 em malha), usadas em rodovias, pavimentação da pista do aeroporto, reduzir o ruído e prolongar a vida útil do serviço.
- Reciclagem de produtos de borracha: fornecendo matérias -primas de borracha de borracha de tamanho de partícula personalizadas para recaução de pneus, vedações, folhas de borracha industrial etc., reduzindo o custo de novos materiais.
- Cenário de economia circular: classificação síncrona de fios de aço (refino de aço) e fibras de nylon (materiais auxiliares têxteis), percebendo “recursos de componentes completos” de pneus residuais.
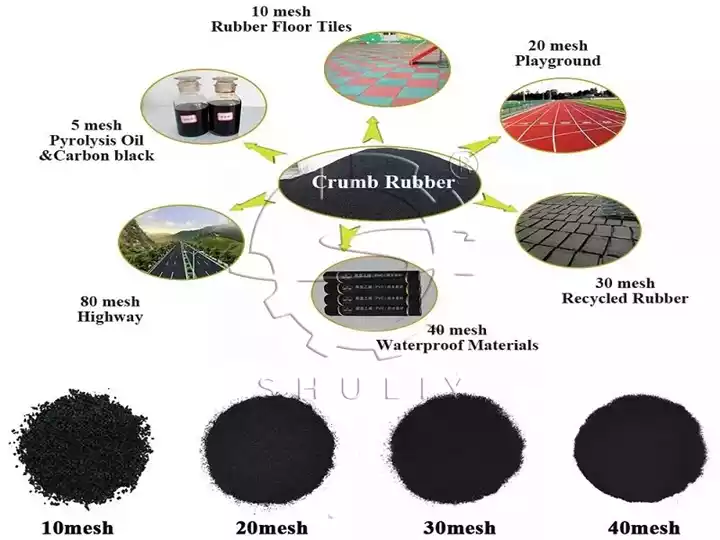
Composição estrutural da unidade de moagem e peneiração de borracha
Componentes Principais
The rubber powder crusher machine adopts integrated linkage design, the core consists of main feeder (uniformly conveying rubber blocks), rubber crusher (high-speed hammer impact crushing), main/secondary vibrating screen and coarse/fine magnetic separator (two-stage magnetic separation to remove impurities of steel wire), supplemented by the discharge port diversion device to realize the accurate sorting of rubber powder, steel wire and nylon fiber.
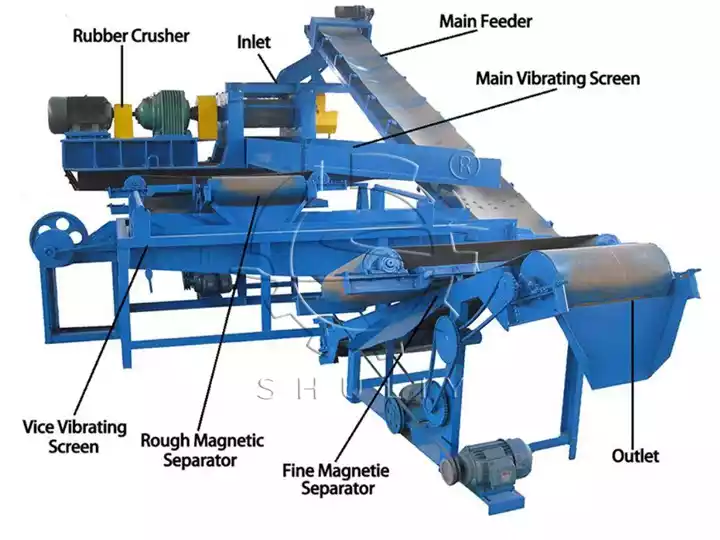
Fluxo do Princípio de Funcionamento
- Transferimento da matéria-prima: O bloco de borracha entra no triturador de borracha através da entrada e é esmagado em partículas de ≤20 mm pelo impacto de martelos de alta velocidade.
- Tela vibratória principal: rastreie as partículas de borracha, 5-40 malha em pó fino em pó diretamente, partículas grossas (> 40 malha) no esmagamento secundário da tela vibratória secundária.
- Tela vibratória de vice: o material grosso residual após a triagem secundária retorna ao triturador para reciclagem, garantindo a quantidade total de conversão fina.
- Separador magnético grosso: adsorção preliminar de grandes partículas de arame de aço (como fio de aço residual de contas de pneu).
- Separador magnético fino: remove as impurezas de metal no nível da migalha em profundidade para garantir a pureza do pó de borracha (taxa de impureza <0,5%).
- Saída do produto acabado: O pó de borracha limpo é descarregado da porta de descarga e o fio de aço e a fibra de nylon são classificados e reciclados simultaneamente.
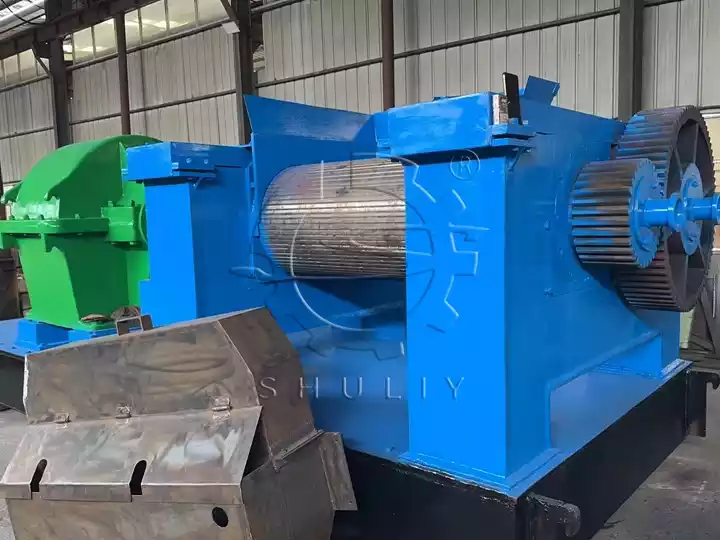
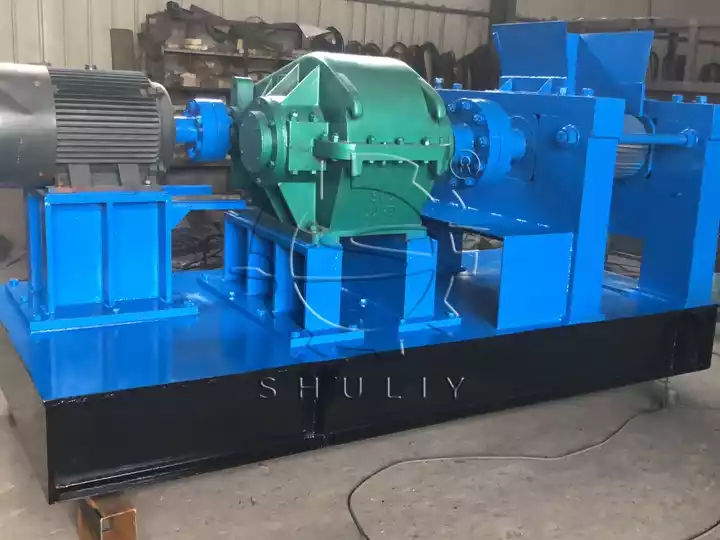
dados técnicos do moedor de pó de borracha
Esta série de máquinas de triturador de borracha em pó possui principalmente os seguintes modelos, e a capacidade de processamento por hora varia dependendo do modelo. Você pode escolher o modelo de acordo com o tamanho e a capacidade de borracha que você precisa, mais modelos como abaixo.
Modelo no. | Capacidade (kg/h) | |
Linha SL-350 | 10 malha (2,5 mm) | 250-300kg/h |
20 malha (1,25 mm) | 180-230 kg/h | |
30 malha (0,83 mm) | 150-210 kg/h | |
40 malha (0,63 mm) | 80-120 kg/h | |
Linha SL-400 | 10 malha (2,5 mm) | 400-500kg/h |
20 malha (1,25 mm) | 300-350kg/h | |
30 malha (0,83 mm) | 240-280kg/h | |
40 malha (0,63 mm) | 150-175kg/h | |
Linha SL-450 | 10 malha (2,5 mm) | 500-600 kg/h |
20 malha (1,25 mm) | 400-500 kg/h | |
30 malha (0,83 mm) | 350-450 kg/h | |
40 malha (0,63 mm) | 200-250 kg/h | |
Linha SL-560 | 10 malha (2,5 mm) | 900-1000 kg/h |
20 malha (1,25 mm) | 600-700 kg/h | |
30 malha (0,83 mm) | 450-550 kg/h | |
40 malha (0,63 mm) | 300-350 kg/h | |
Linha SL-560D | 10 malha (2,5 mm) | 1500-1600 kg/h |
20 malha (1,25 mm) | 1200-1300 kg/h | |
30 malha (0,83 mm) | 1000-1100kg/h | |
40 malha (0,63 mm) | 800-900 kg/h | |
Linha SL-660 | 10 malha (2,5 mm) | 2100-2300kg/h |
20 malha (1,25 mm) | 1600-1700kg/h | |
30 malha (0,83 mm) | 1200-1300kg/h | |
40 malha (0,63 mm) | 900-1000kg/h |
A linha de reciclagem de máquina de britagem em pó de borracha com design sinérgico modular, para obter “bloco de borracha → borracha em pó → classificação” todo o processo de loop fechado de alta eficiência.
Se precisar de construir toda a cadeia de regeneração de pneus, também podemos fornecer o separador de arame de aço de pneus (descascamento não destrutivo do arame de aço da talão), máquina de corte/bloqueio e outros equipamentos, para criar uma solução completa de "desmontagem – triagem – trituração". Clique aqui para obter uma solução personalizada que se ajuste à sua capacidade e orçamento!