Recentemente, nossa empresa e um cliente do Sudão do Sul concluíram um projeto de cooperação de máquinas de reciclagem de plástico PET, incluindo uma linha de britagem e lavagem de PET e uma linha de pelotização de PET. Através desta cooperação, a perspectiva do cliente no domínio da economia da reciclagem de plástico foi ainda mais fortalecida. Abaixo estão os detalhes do projeto e da instalação no local.
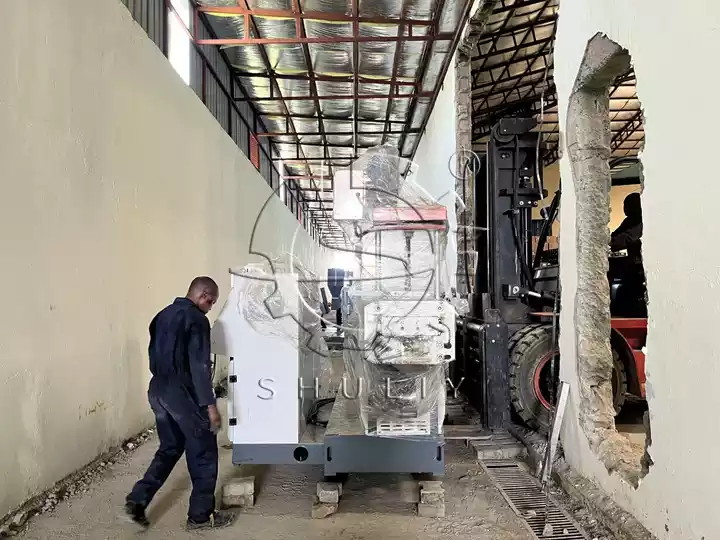
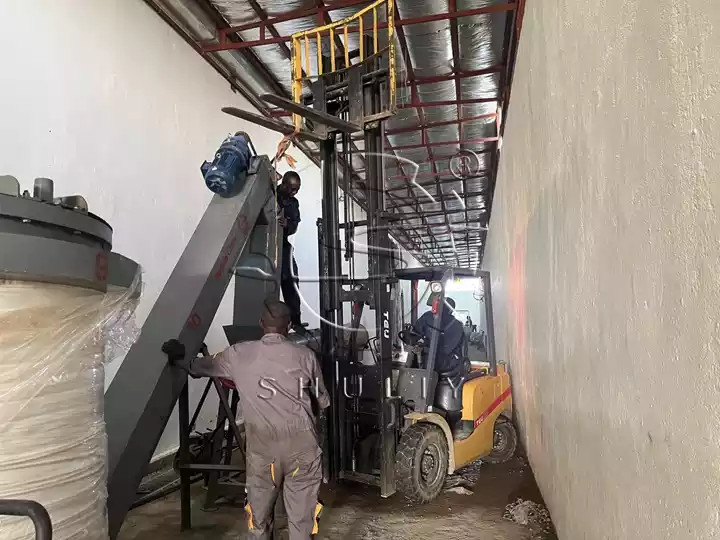
Contexto e necessidades do cliente
O cliente do Sudão do Sul tem profunda experiência no campo da economia da reciclagem de plástico e o seu negócio principal centra-se na reciclagem e reutilização eficiente de resíduos plásticos.
Vendo o enorme potencial do mercado de tratamento de resíduos plásticos, o cliente decidiu expandir o seu âmbito de negócio para transformar mais resíduos plásticos em recursos reutilizáveis. Para atender a essa demanda, o cliente escolheu nossa linha de produção de máquinas para reciclagem de plástico PET após uma investigação e avaliação aprofundadas.
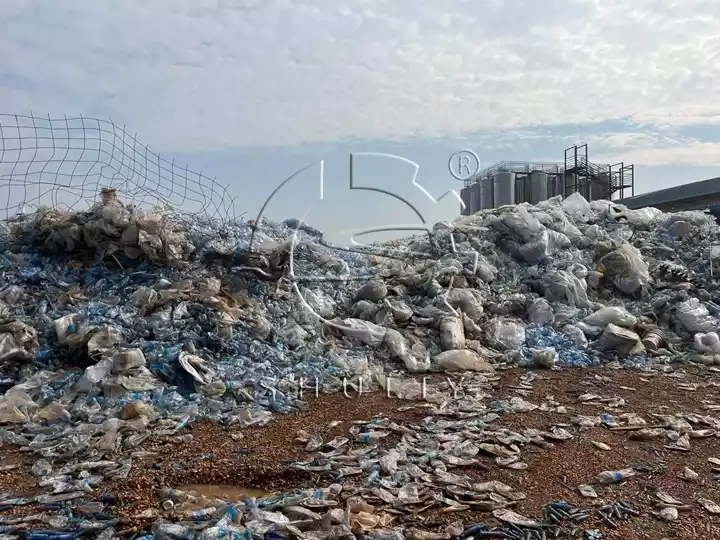
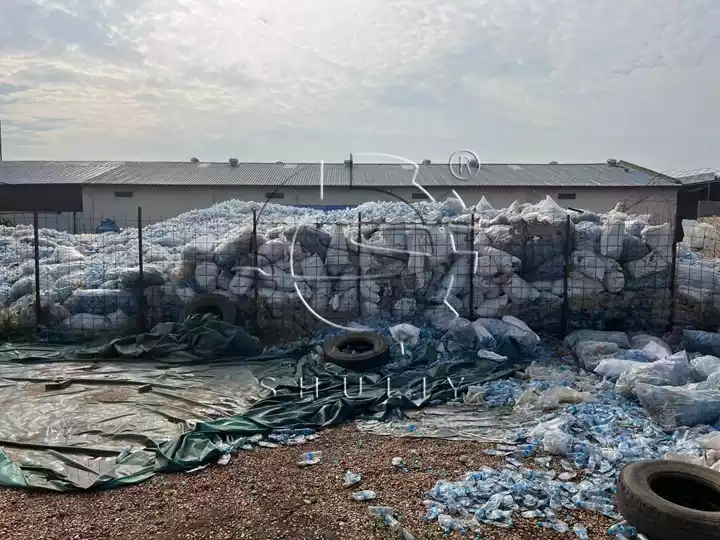
Expectativas e objetivos do cliente
Ao apresentar nossas máquinas, o cliente espera converter uma grande quantidade de resíduos de garrafas PET, materiais de embalagem e outros resíduos plásticos em pellets reciclados de alta qualidade.
Esses pellets reciclados serão utilizados principalmente na produção de fibras têxteis, materiais de embalagem e materiais de construção, desenvolvendo ainda mais um amplo espaço de mercado.
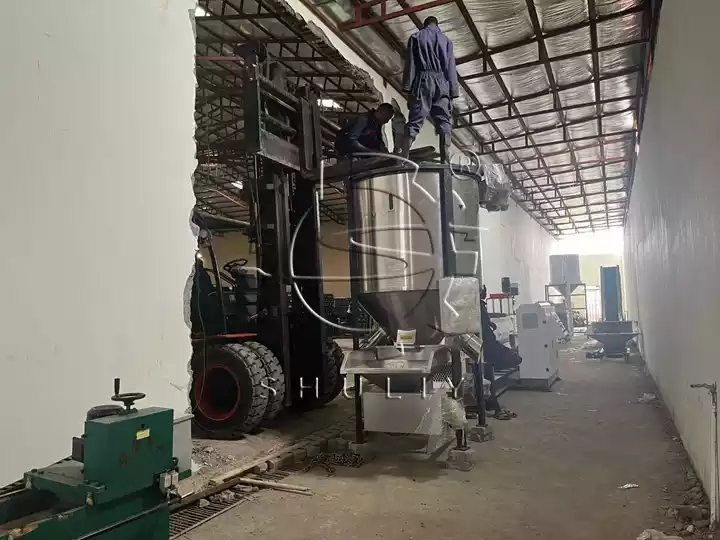
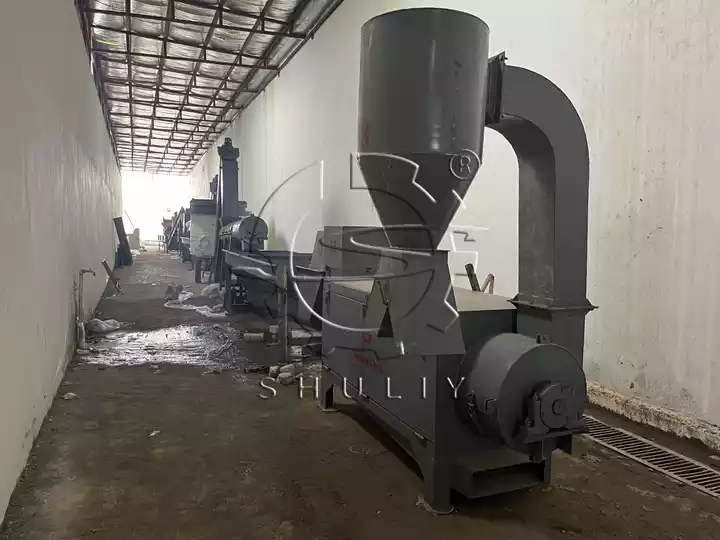
Informações sobre máquinas de reciclagem de plástico PET
Com uma capacidade de processamento de até 500kg/h, nossa linha de trituração e lavagem de PET pode separar e lavar rapidamente os resíduos mistos de PET para garantir sua pureza para processamento subsequente. A linha de produção de pelotização de plástico PET conectada pode converter eficientemente as flocos de PET limpos em pellets reciclados com uma produção estável de 3-4 toneladas por dia.
Essas duas linhas funcionam bem juntas para fornecer aos clientes uma solução integrada de reciclagem de plásticos para atender às suas necessidades de produção em larga escala.
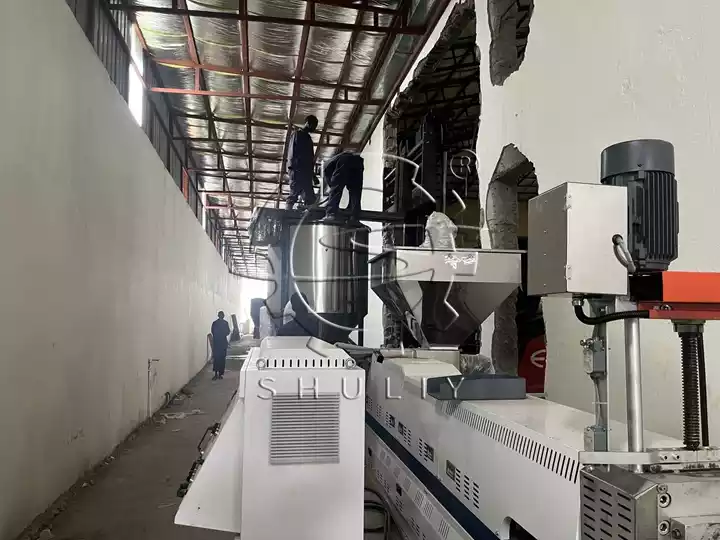
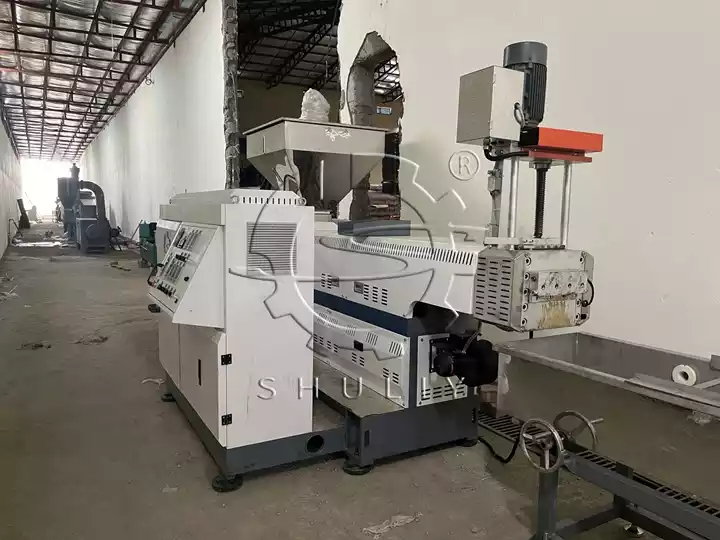
Instalação e suporte técnico
Para garantir o funcionamento suave do equipamento, enviamos técnicos experientes para o local do cliente em Sudão do Sul para realizar a instalação e comissionamento no local.
Durante o processo de instalação, os técnicos acompanharam todo o processo para garantir que cada equipamento pudesse funcionar de forma estável e forneceram treinamento operacional detalhado para a equipe de operação do cliente.
Com a cooperação ativa do cliente, todo o processo de instalação foi muito tranquilo e o equipamento foi rapidamente colocado em produção normal.