The plastic granulation machine is essential in the plastics recycling industry. It efficiently cuts waste plastic products into small pellets, known as “recycled material” or “plastic chips,” which are crucial for the recycling process. In this article, we will discuss the functions of plastic granulators, their applications, and tips for selecting the right equipment.
The role of plastic granulation machine
The primary role of a plastic pelletizer is to minimize the size of plastic waste, facilitating easier processing and recycling. The plastic recycling process typically involves the following steps:
- Sorting and Separation: different types of plastics (like PET, HDPE, PP, etc.) are sorted to enhance the quality of recycling.
- Size Reduction: plastic granulator machines are used to chop plastic scrap into smaller pieces, making it simpler to melt or reprocess.
- Cleaning & Drying: stains, labels, or residues are removed from the plastic’s surface to ensure the recycled material’s purity.
- Pelletizing & Recycling: the crushed plastic is melted and reshaped into pellets for the manufacturing of new products.
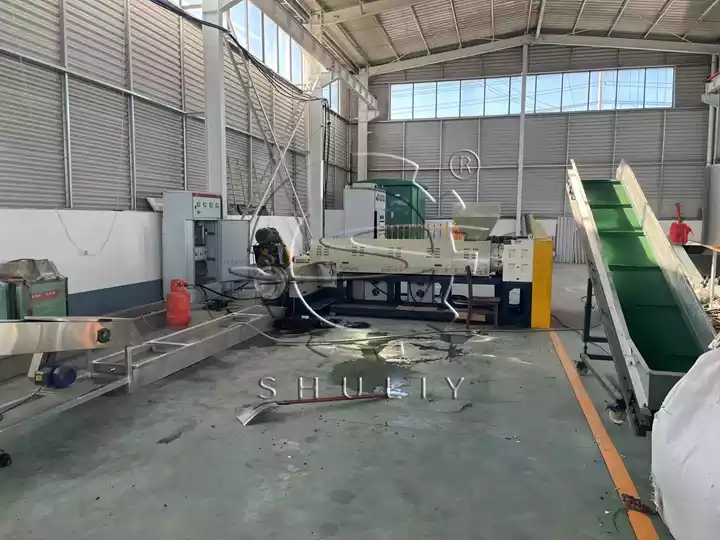
Plastic granulation machines play a crucial role in this process, particularly for plastics processors involved in injection molding, blow molding, and extrusion. They enable the direct recycling of waste materials from production, such as runners (sprues) and discarded parts, significantly reducing raw material losses.
What materials can the Plastic Pelletizer process?
Plastic granulation machines are designed to work with a variety of plastic types, including but not limited to:
- PET (Polyethylene Terephthalate) – commonly found in beverage bottles and food packaging.
- HDPE (High Density Polyethylene) – used for pipes, bottles, and plastic drums.
- LDPE (Low Density Polyethylene) – often seen in plastic film, shopping bags, and agricultural film.
- PP (Polypropylene) – utilized in appliance housings, automotive parts, and plastic seats.
- uPVC (unplasticized polyvinyl chloride) – frequently used in construction materials like window and door frames, as well as drainage pipes.
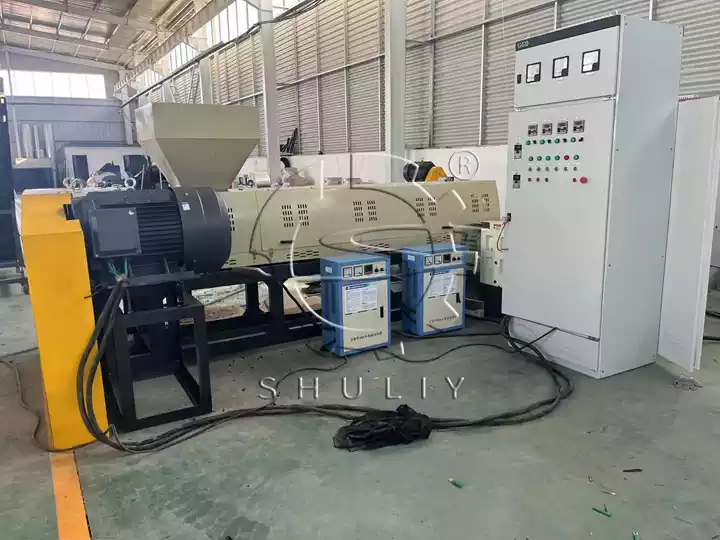
Plastic pelletizing machines come in different sizes and models, with varying capacities for handling different types of plastic. For instance, small granulators are ideal for processing plastic bottle caps and film edges, while larger granulators can manage waste plastic pipes, car bumpers, and other sizable plastic products.
How to choose the right plastic pellet machine?
Choosing the right plastic granulator should be based on your specific application needs. If you’re uncertain about which machine is the best fit, consider these factors:
- Material type: different plastics vary in hardness, toughness, and thickness, so it’s important to match them with the right pelletizer blade and power.
- Processing capacity: select equipment with the appropriate power and capacity based on your output requirements. For instance, small to medium-sized factories typically need machines that handle tens to hundreds of kilograms per hour, while larger recycling plants may require granulators capable of processing tons per hour.
- Finished product requirements: if you need further granulation or reprocessing, opt for a granulator that produces a uniform particle size to ensure the quality of the final product.
- Energy consumption and maintenance: choosing energy-efficient equipment can help lower long-term operating costs, and it’s also wise to consider how easy the equipment is to maintain to boost productivity.
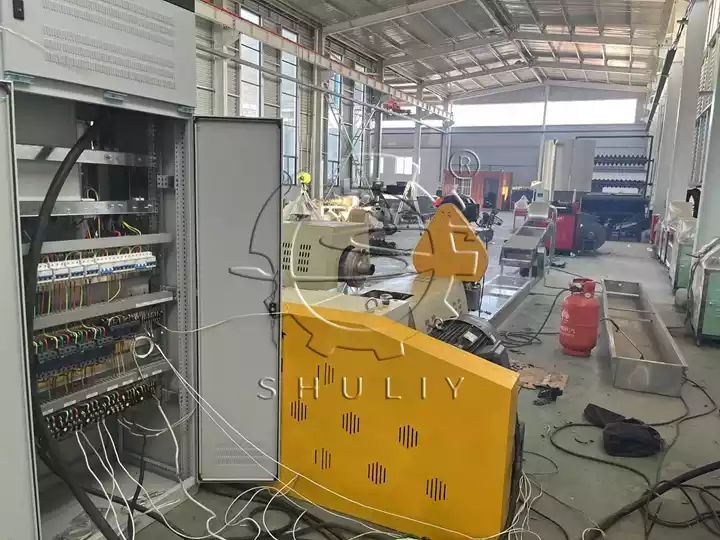
If you’re still unsure about which plastic granulation machine for recycling will meet your production needs, feel free to reach out to us anytime. Our expert engineers can help you find the most suitable equipment based on your material type, capacity requirements, and budget.