The primary process for a PET bottle recycling line is the washing and shredding of post-consumer PET bottles into rPET flakes. These flakes can be remanufactured into food-grade chips, PET felts, and PET fibers. This type of rPET flakes meets FDA standards for direct contact with food and beverages.
A PET bottle recycling machine production line usually includes a series of equipment such as washing, crushing, de-labeling, separating, and drying. It has an outstanding capacity of 500kg to 6000kg per hour. Here in Shuliy Manufacturer, we can tailor to your requirements and make PET recycling machines to be cost-effective and technologically reliable.
raw materials for PET Bottle recycling line
PET bottle recycling line is suitable for raw materials mainly including but not limited to the following types:
- Beverage bottles: e.g. mineral water bottles, carbonated beverage bottles, fruit juice bottles, etc.
- Edible oil bottles: PET bottles are also commonly used to package edible oil products.
- Cleaner bottles: containers for household products such as detergents and washing agents.
- Cosmetic bottles: such as shampoo, conditioner, shower gel, and other cosmetic containers.
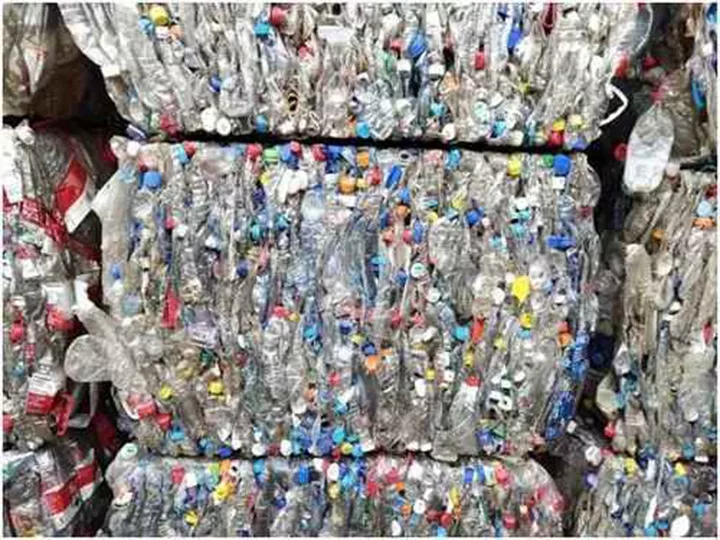

the final product you can get
PET plastic bottles are not waste. It is one of the most used plastic packaging materials because it has good properties and is highly recyclable, with potential for subsequent use.
PET flakes can be heated and molded into a variety of shapes. PET has a lower melting temperature than alternatives such as glass and aluminum. This makes it easy and sustainable to convert PET flakes into more PET packaging in a closed loop.
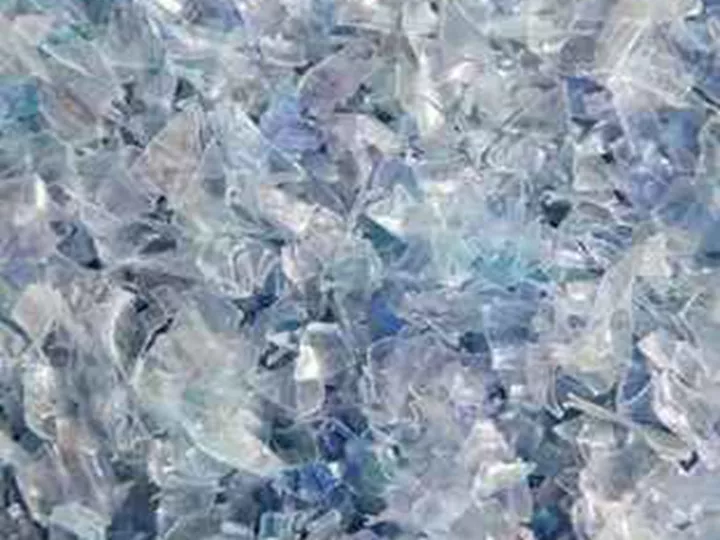
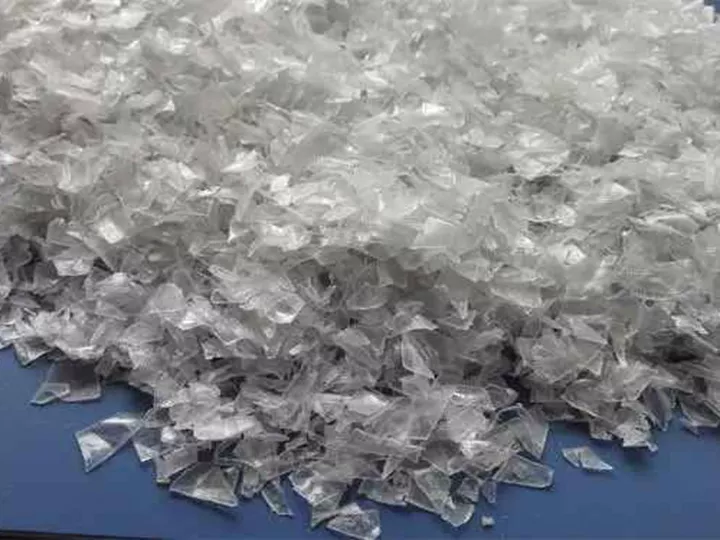
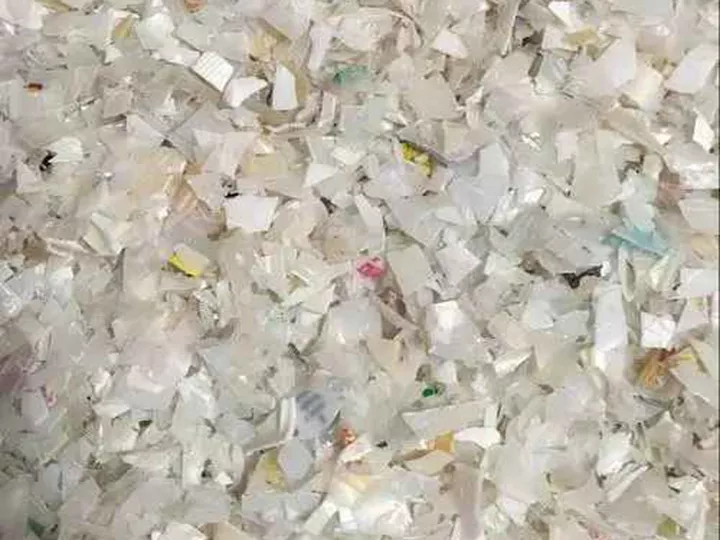
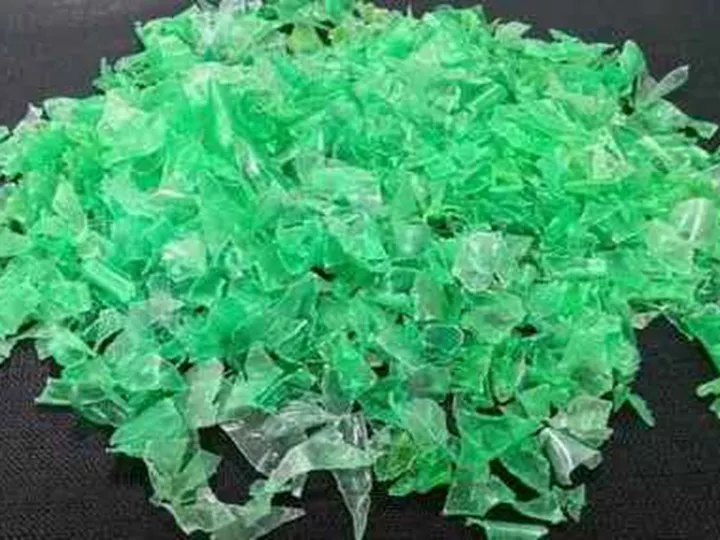
PET flakes reforming prospects
These recycled PET flakes can be sent to the packaging industry for use. These flakes are made into preforms, which are then made into new bottles.
These PET preforms are heated and then molded into the correct size and shape. This completes the bottle-to-bottle cycle and ensures a more sustainable future for the packaging industry.
Recycled PET is completely safe for use in food packaging and has been approved by organizations and governments around the world.
Customized Service
We can customize the configuration, output, and appearance of the PET bottle recycling line according to the customer’s specific needs. We also design the right program according to the size and layout needs of the customer’s plant.
Regardless of the size of the plant, we can make the best use of the space for you to ensure efficient operation of the equipment and maximize production efficiency. Through well-designed solutions, we can optimize workflow and improve equipment utilization, thus bringing greater convenience and benefits to your production operations.
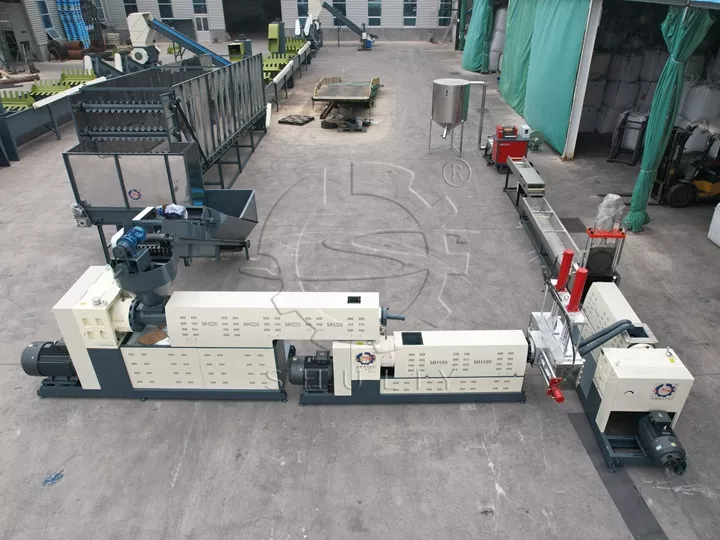
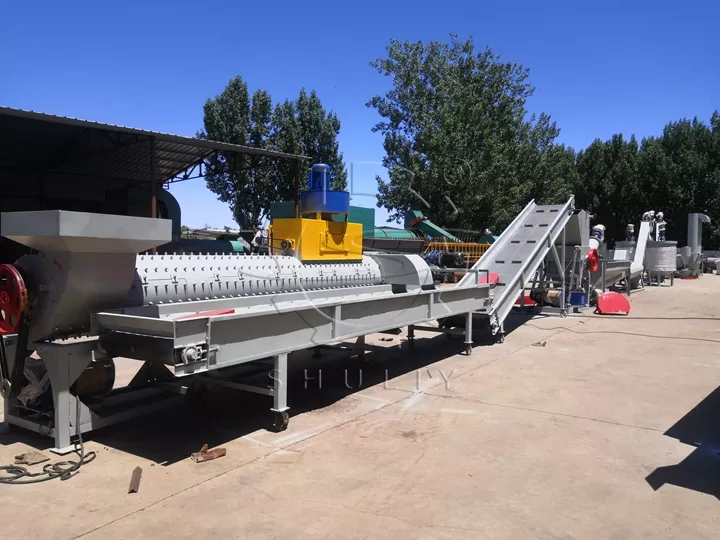
workflow of PET bottle recycling plant
Completing the recycling of used plastic bottles involves a series of steps including raw material conveying and sorting → crushing → soaking and washing → de-watering → pelletizing and cutting → packaging and discharging.
This PET bottle recycling line workflow can vary, depending on the type of equipment and production needs. Overall, however, these steps represent the typical operation of a plastic bottle washing and recycling line.
main machines of plastic bottle washing plant
If the raw material is in the form of compressed bundles, the plastic bottles first need to be dispersed one by one using a bale opener. For more information on exactly how this machine works, you can check out: Plastic Bale Opener For PET Bottles Separating Machine.
label removing machine
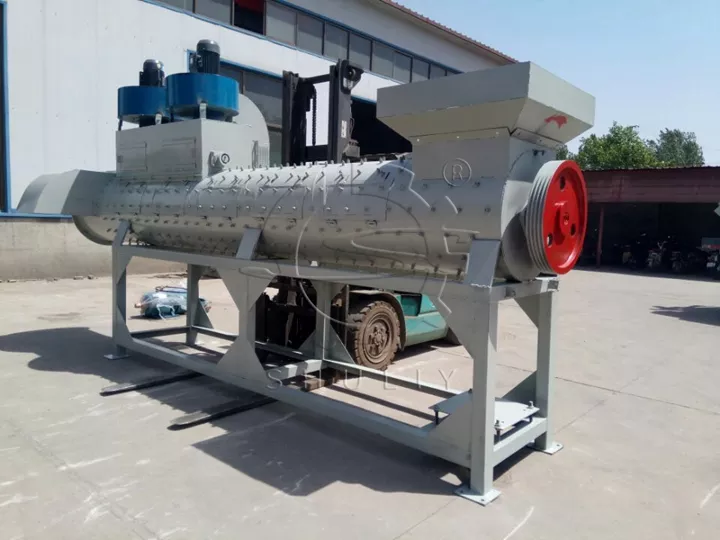
Labeled, trademarked or printed bottles contain glue or ink that can affect subsequent PET bottle recycling line processing steps and product quality. De-labeling helps ensure that the PET pellets produced are of high quality and free of impurities. Label removal rates of 98%-99% for round bottles and 85%-90% for flat bottles can be achieved.
PET plastic crusher
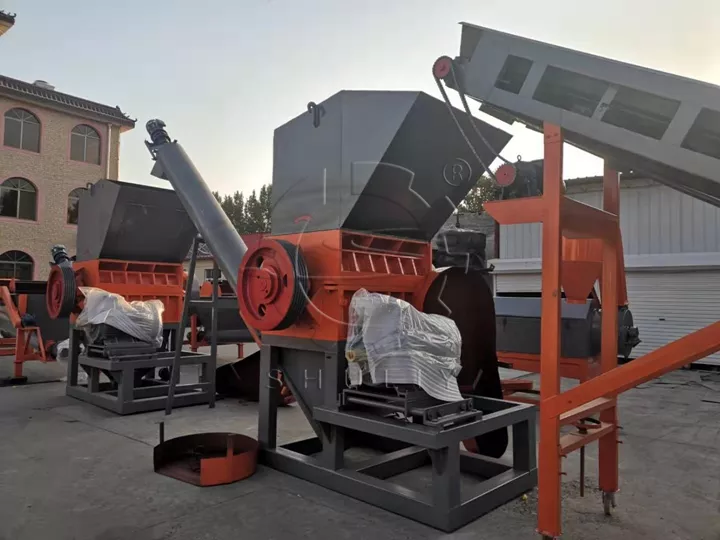
Raw materials are sent to the crusher by an elevating conveyor. The importance of this step in the PET bottle recycling line is that it reduces the size and facilitates the cleaning process. Smaller PET flakes make it easier to remove dirt and residues during the washing phase.
washing and sorting tank
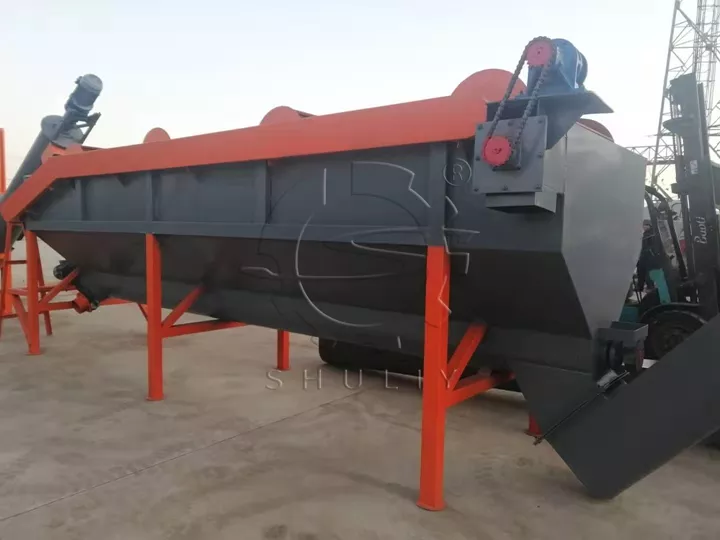
The line goes through a total of four washes, with the washing and sorting tank serving as the first wash. In addition, this sorting separates light impurities, such as labels, caps, etc., as well as removes heavy impurities, such as metal, glass, etc., resulting in purer PET flakes.
hot washing tank
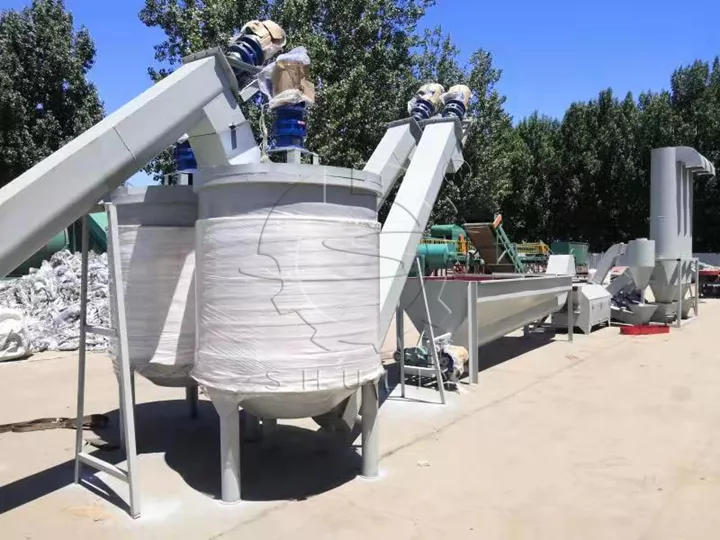
Hot wash tanks are processed at high temperatures to kill and remove microorganisms, bacteria, and fungi that remain on plastic bottles. And it removes odors, which helps to ensure the hygiene and safety of recycled plastic chips. The machine uses hot water and cleaning agents, usually at temperatures of 85°C to 95°C.
friction washing machine
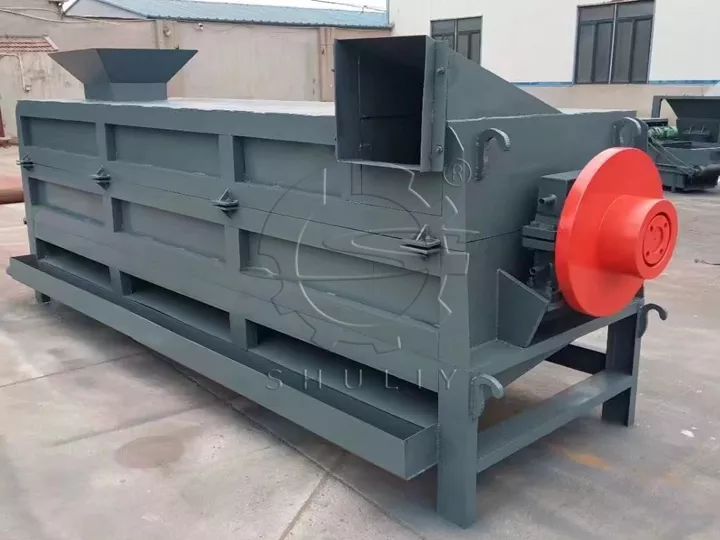
Using friction and a high-velocity water stream, plastic debris is deeply cleaned and contaminants such as residual stains, grease, and dirt are removed, ensuring that hygiene, quality, and reusability standards are met.
dewatering machine
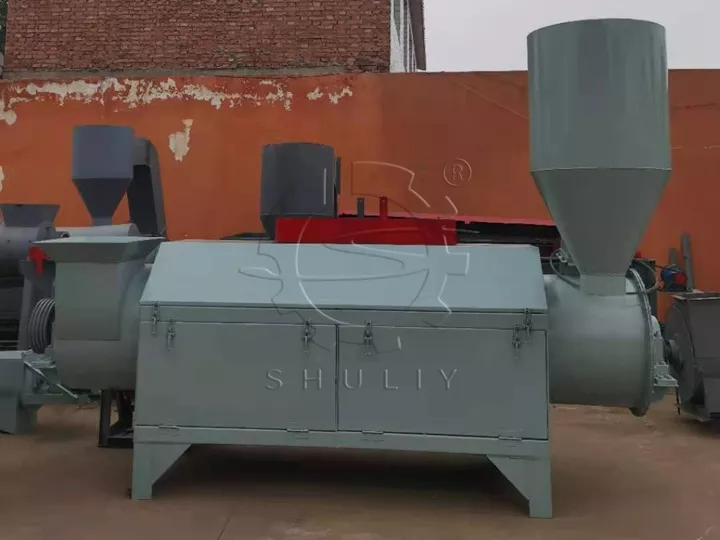
Utilizes the principle of high-speed rotation to dewater and remove excess water from washed wet plastic debris.
PET bottle recycling washing line price
Shuliy’s PET bottle recycling line is priced with a clear competitive advantage. We have always been committed to providing high-performance and high-efficiency recycling equipment while keeping the price relatively affordable.
In addition, we offer a wide range of line models and configurations to meet different customer needs and budgets. We ensure that our customers get high-quality equipment at the most reasonable price.
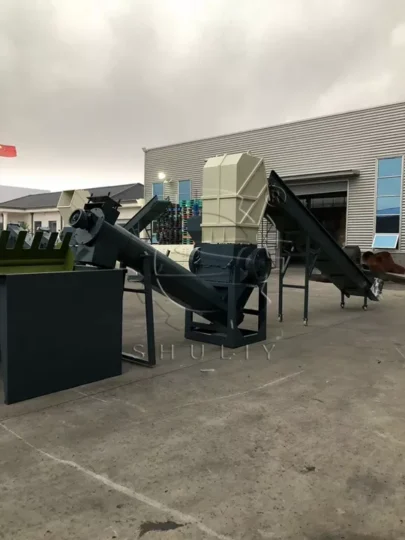
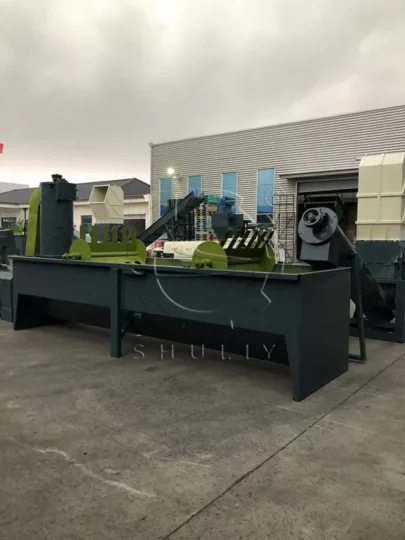
High level of popularity
Plastic PET bottle recycling line machines are in high demand in many countries. These include countries like Malaysia, Ethiopia, the USA, Germany, Japan, India, Brazil, Mexico, Tanzania, Nigeria, the UK, France, and Australia.
These countries usually face a huge plastic waste problem and therefore have a high demand for advanced recycling equipment and technology. Additionally, government policies and regulations in some countries encourage and support plastic bottle recycling, further fueling demand growth.