の プラスチック顆粒押出機 廃シルク、廃フィルム、廃織布袋、廃ペットボトル、廃プラスチックドラム、プレート、および粉砕材料に適したプラスチックペレット化装置の一種です。それでは、これらの廃棄物の再生可能な粒子を実現するには、どのようなプロセスを経る必要があるのか、引き続き見ていきましょう。
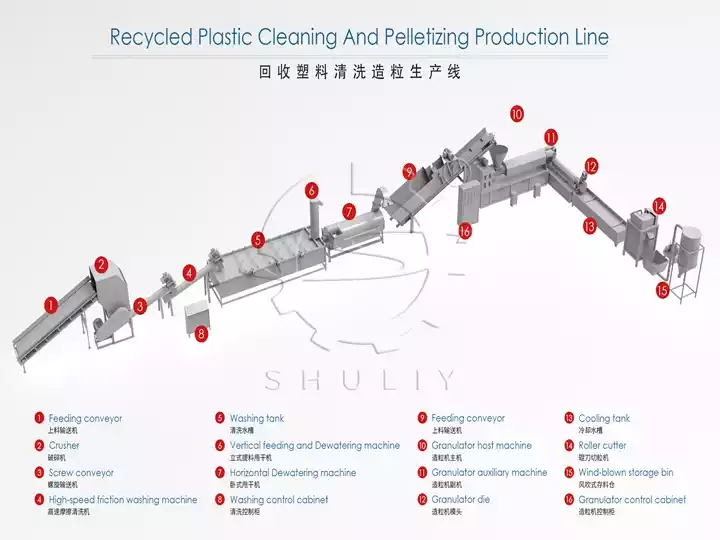
プラスチック顆粒押出機 原料準備
の プラスチック顆粒押出機プロセス PP、PE、PVC、EVA、その他の種類のプラスチックなどの原材料の準備から始まります。まず第一に、 コンベアベルトローダー 破砕する材料をプラスチック破砕機に運ぶために使用されます。

プラスチックの粉砕と洗浄
材料を粉砕、洗浄する前処理。
- プラスチック破砕機—- 大きな原料をその後の作業のために小さな断片に分解します。
- 摩擦洗浄槽−−粉砕物を強力に摩擦洗浄する場合。
- リンスプール1 —- 廃プラスチック粉砕物を洗浄し、沈殿物や不純物を除去します。洗浄された材料は次の洗浄槽に送られます。
- 洗浄槽2 — 廃プラスチックのスクラップを再度洗い流します。
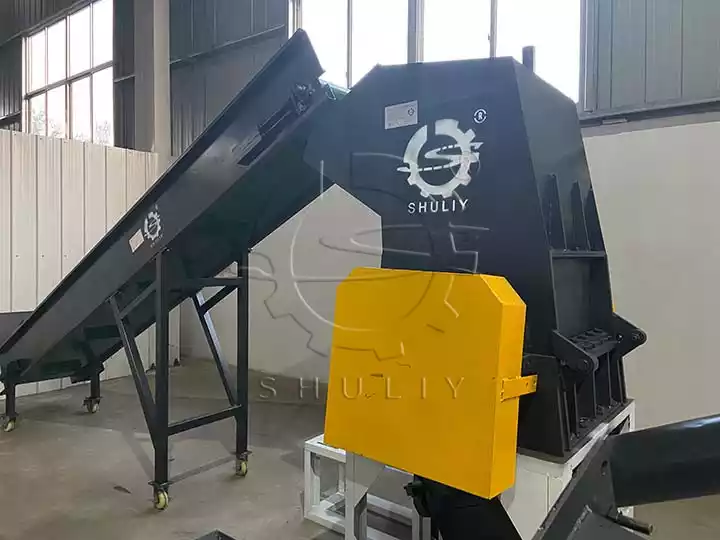
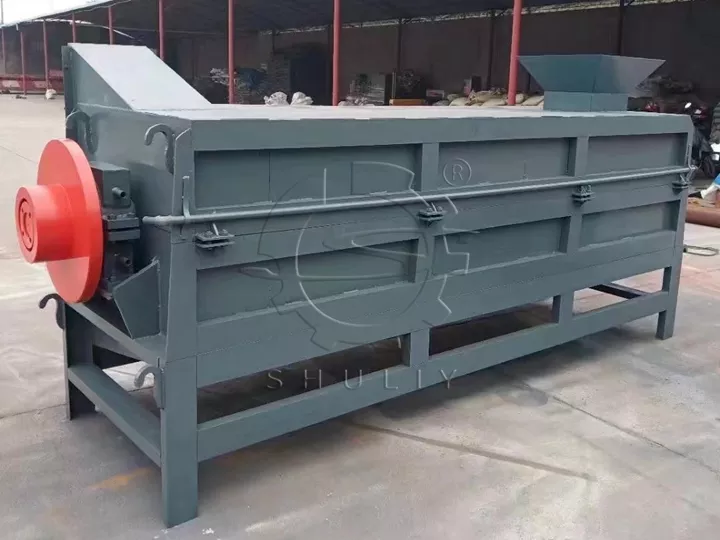
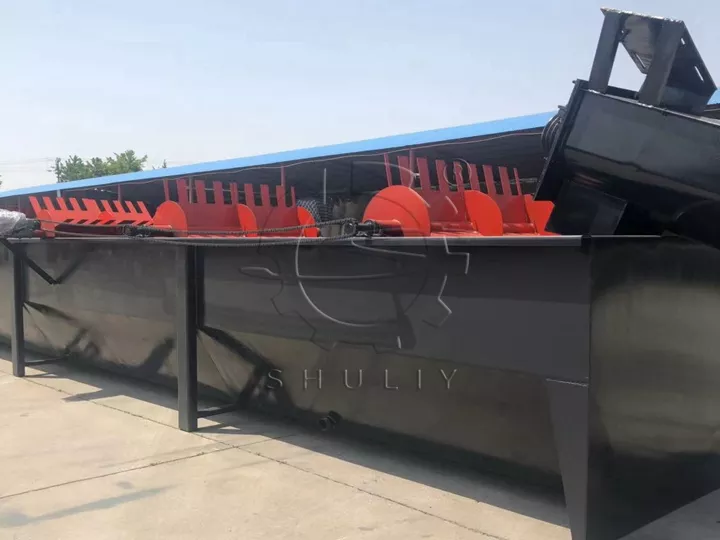
脱水と給餌
- 乾燥機 — 洗浄した材料を脱水し、乾燥させます。ペレット化される材料は強制フィーダーに自動的に供給されます。
- 強制給電装置 — 材料をプラスチックペレタイザーのメインマシンに均一かつ整然とした方法で供給します。
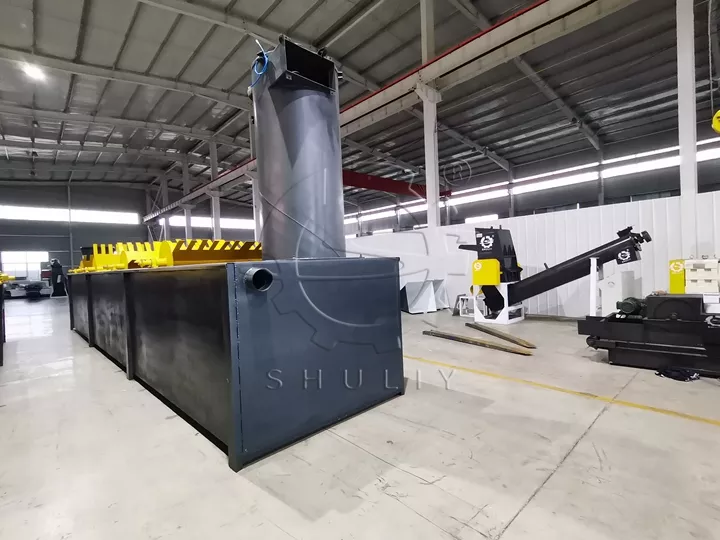
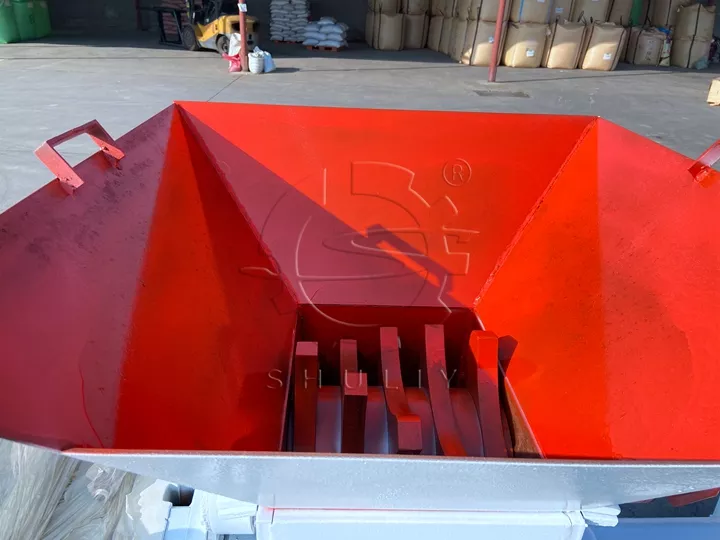
ペレット化と冷却
- プラスチックペレタイザー メインマシンとバイスマシン – ペレット化、押出、延伸プロセスを実現します。
- ステンレス製冷却水タンク — ダイヘッドから押し出されたプラスチックストリップを冷却するため
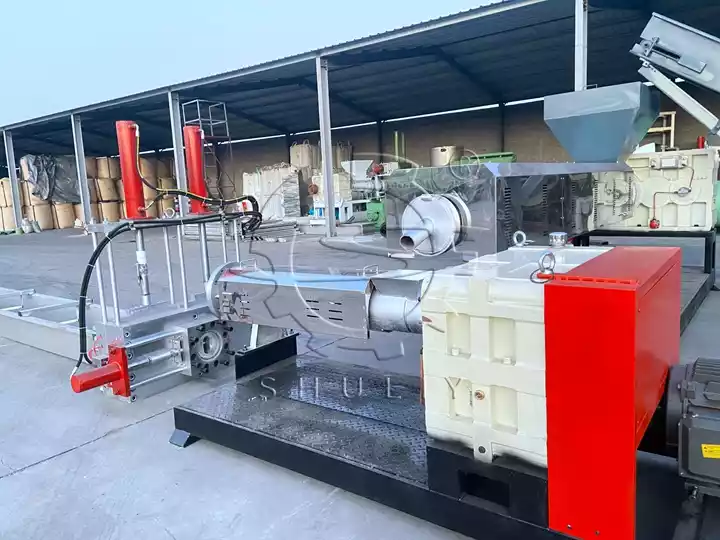
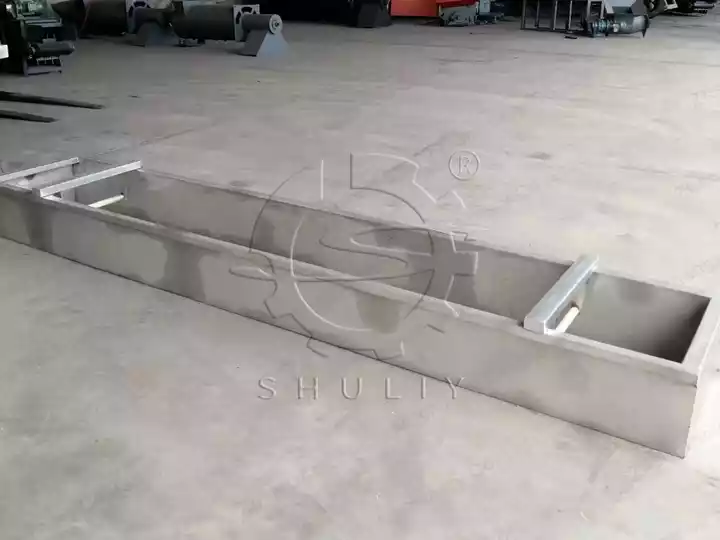
この効率的なプラスチック 顆粒 押出機プロセスは、生産効率を向上させ、エネルギー消費を削減するだけでなく、プラスチックリサイクル業界において環境に優しい役割も果たします。当社のプラスチック造粒装置にご興味がございましたら、お気軽にお問い合わせください。