Our factory has successfully completed the production of a plastic pellet mill machine and shipped it to Iran. The equipment will be used by the customer to recycle and process EPS foam plastic, promoting the efficient reuse of local plastic resources.
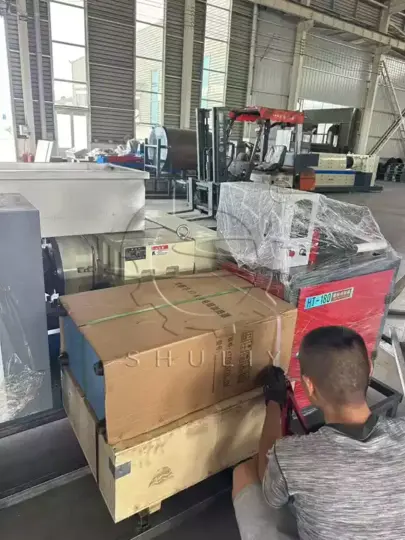
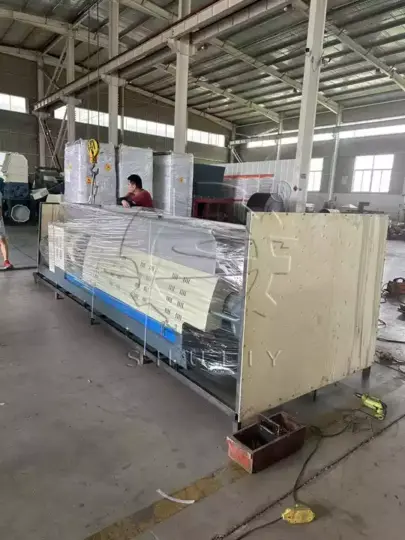
Customer confirmation and Machine Testing
The Iranian customer is primarily engaged in the recycling and reuse of foam plastic. The plastic pelletizer ordered this time is specifically designed for processing EPS foam plastic.
After the equipment was completed, our factory’s technical team conducted on-site trial operations using raw materials provided by the customer.
During the trial operation, the foam plastic underwent processes such as crushing, melting, extrusion, cooling, and pelletizing, successfully transforming into high-quality plastic pellets with excellent forming results and no machine blockages.
We filmed the entire trial operation process and sent the video to the customer for review. After viewing the video, the customer gave high praise and expressed great satisfaction with the equipment’s operational efficiency and product quality.
features of plastic pellet mill
The plastic pelletizer recycling machine shipped this time has the following main features:
- High-efficiency recycling of lightweight materials such as EPS foam plastic.
- Intelligent operation, including automatic feeding, melting, and extrusion, reducing labor costs.
- Uniform finished pellets, facilitating subsequent plastic product production.
- Low overall energy consumption, with a production capacity of 150-300 kilograms per hour, suitable for small and medium-sized plastic recycling plants.
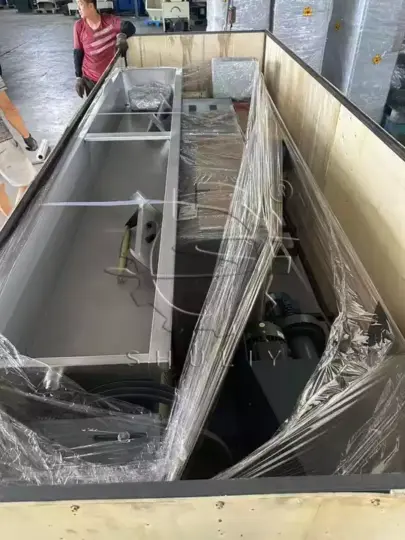
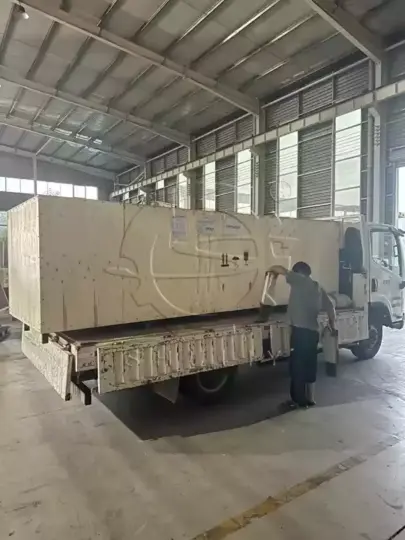
Efficient and safe packaging and shipping
To ensure the equipment remains undamaged during long-distance transportation, our factory employed a comprehensive packaging method including multi-layer stretch film wrapping, wooden box securing, and anti-corrosion treatment.
After packaging was completed, the equipment was successfully loaded onto a truck and shipped to Iran, with an expected arrival at the customer’s factory shortly for official use.